Prequel (added Nov 6, 2018): Have just discovered that my targeted criticisms of the 1978 STURP initiative were voiced way back in May 2015 on my now long-in-the-tooth science buzz site.
(That site having been started in 2009, some 3 years prior to this one).
So why did I fail to recall it?
Answer: apart from this 74-year old’s increasing senility, cue intermediate-term memory loss (short term probably close on its heels), it’s probably because they were tacked onto the end of an otherwise highly experimental, hands-on posting. It was to do with the details of Model 6 (then deploying a chemical means – nitric acid – to develop the yellow colour of a flour imprint, subsequently replaced by heat).
That diversion into STURP’s alleged shortcomings would now be lost in the mists of time. However, yesterday I perchance came across the scathing (ill-considered?) reception given by Dan Porter in May 2015 on his long-retired site to those candidly-stated views of mine regarding STURP and much else besides (given this site is/was a real-time account of scientific, experiment-based research in progress, from start – Model 1- 2011 – to finish, Model 10 – 2015- possibly, dare one suggest unique in the history of the internet ? )…
Link

(I don’t suppose Dan is reading this, but if he is, then here’s a belated reply, given I chose not to respond to his posting).
I stand by every word I wrote in 2015 regarding STURP – a hopelessly mismanaged project if ever there was, lacking direction and focus (except for that banal ‘just a painting’ obsession, showing a blind spot for the largely self-evident conclusion that should have been drawn by any researchers in full command of their scientific faculties, specifically from the negative, i.e. light/dark -reversed body image – namely an IMPRINT, indeed CONTACT IMPRINT, hardly a free-hand painting, far less, as STURP-leader Dr. John Jackson’s would have us believe, a 1st century internally- body-generated supernatural radiation-generated Resurrectional ‘selfie’).
Shame the Gospels provide no hint of such an event having occurred!
(So why did the Risen Christ bother to re-make contact with his disciples “on the road to Emmaus etc” to show he was still of this world, displaying wounds on hands etc to the Doubting Thomas etc. prior to the final Ascension (the latter surely a more credible scenario for a flash of body-consuming radiation – NOTE: Ascension not Resurrection?)
Site banner? See Appendix.
—————————————————————–
End of prequel: original posting starts here
Let’s begin with a cut-and-paste from a comment by the Editor of shroud.com , i.e. Barrie M. Schwortz, perhaps better known as President of STERA (Shroud of Turin Education and Research Association). Schwortz was previously 1978 STURP’s Documenting (not to be confused with separate Scientific) Photographer. It was on his June 2018 Newsletter, shortly to be updated we’re told by an October 8 (to commemorate the controversial STURP’s 40th Anniversary|)

It’s the final highlighted sentence that is the subject of this current posting. Apols for the size. It reads: “I think you will find it enlightening as it clearly demonstrates the thoroughness and care that STURP exhibited in planning their research. It creates a benchmark and provides an example that future Shroud researchers can use to carefully plan their own work”.
How’s that for a photographer attempting to tell current follow-up scientists (like myself!) how to do their job, attempting to make good the numerous shortcomings of the 78 visit to Turin, laden down with shiny gee-whizz hardware !
Such presumption of superiority! Such arrogance!
More to follow (oh yes, much, much more!). It’s time for this retired biomedical scientist/Shroud investigator (the latter of some 7 years standing) to tell it the way it is.
(My studiously-ignored Model 10 – some 6 years in the making – may get a brief look-in. But that’s not the primary purpose of the exercise, which is now largely to put an unflattering spotlight on sindonology’s largely pro-authenticity promoting, and all-too-often anti-authenticity-sniping modus operandi!).
Foretaste: let’s be clear about one thing.
STURP got it completely, and I mean COMPLETELY wrong as regards that defining NEGATIVE , i.e. tone-reversed body image, one which it largely ignored. Indeed, it failed in its 1981 Summary to make a single mention of the term “imprint” – the production of which guarantees a 100% negative image – choosing instead to focus on consciously artist- directed “paint” and “painting”. ( Merely a painted image? That’s what one refers to currently on the internet as an easy-to-knock- down “strawman’ target”.)
If you think I’m overstating my case, dear reader, then ask yourself this question. What’s the most defining characteristic of the TS body image , as discovered in the last 120 years, at least initially, pre those supposedly “unique 3D characteristics”? Yes, it’s surely the negative, tone-reversed character, as shown by Secondo Pia in 1898.
Now search for “negative”in the STURP 1981 Summary. How many mentions? Yes, dear reader: zero, absolutely zero ! And you’ll find scarcely any mentions either in the ‘definitive’ account of the STURP Project, penned by John Heller in his 1983 book, except briefly at the start and at the end.
Why not? Someone kindly explain to me why not, given the reams of pro-authenticity speculation generated these last 120 or so years by that ‘negative ‘ image , in particular, supposed proto-photography via supernatural radiation’, the TS body mage being a “photograph” you realize.
I always thought there was something not quite right, not quite transparently scientific about STURP and its limp 1981 conclusions… It’s not so much what STURP said, as what it didn’t say….
More tomorrow …
Saturday October 6
Today I shall content myself with displaying two items:
First, a screen shot of STURP’s 1981 Summary, taken from the shroud.com site:
—————————————————————————————————————

Second: a modified version thereof, as I believe it should have been written, with my additions etc shown in bold blue, AND highlighting in red those sentences, of parts thereof, which I consider should not have been there, being unsupported or indeed opposed by the limited or selective scientific data.
—————————————————————————————————————
A Summary of STURP’s Conclusions
Editor’s Note: After years of exhaustive study and evaluation of the data, STURP issued its Final Report in 1981. The following official summary of their conclusions was distributed at the press conference held after their final meeting in October 1981:
No EASILY IDENTIFIABLE ARTISTS’ pigments, paints, dyes or stains have been found on the fibrils. X-ray, fluorescence and microchemistry on the fibrils preclude the possibility of paint being used as a method for creating the image BUT THAT DOES NOT EXCLUDE THE POSSIBILITY OF IMPRINTING WITH AN AS YET UNKNOWN IMPRINTING AGENT, NATURAL or MAN-MADE. Ultra Violet and infrared evaluation confirm these studies. Computer image enhancement and analysis by a device known as a VP-8 image analyzer show that the image has unique, three-dimensional information encoded in it. Microchemical evaluation has indicated no evidence of any spices, oils, or any biochemicals known to be produced by the body in life or in death BUT THAT WOULD NOT PRECLUDE A SIMULATED, i.e. “FAKED” BODY SWEAT IMPRINT, SEEMINGLY YELLOWED WITH AGE. It is clear that there has been a direct contact of the Shroud with a body, which explains certain features such as scourge marks, as well as the blood. However, while this type of contact might explain some of the features of the torso, A NUMBER OF US CONSIDER it is totally incapable of explaining the image of the face with the high resolution that has been amply demonstrated by photography.
(ed. I resisted the temptation to strike out the next three sentences, which some might consider are too imprecise, arguably airy-fairy, and ought really to be in a footnote).
The basic problem from a scientific point of view is that some explanations which might be tenable from a chemical point of view, are precluded by physics.
Contrariwise, certain physical explanations which may be attractive are completely precluded by the chemistry.
For an adequate explanation for the image of the Shroud, one must have an explanation which is scientifically sound, from a physical, chemical, biological and medical viewpoint.
(ed. moving on…)
At the present, this type of solution does not appear to be obtainable by the best efforts of the members of the Shroud Team. Furthermore, experiments in physics and chemistry with old linen have failed to reproduce adequately the phenomenon presented by the Shroud of Turin. The scientific concensus (sic) BY SOME BUT NOT ALL MEMBERS OF THE TEAM is that the image was produced by something which resulted in oxidation, dehydration and conjugation of the polysaccharide structure of the microfibrils of the linen itself. Such changes can be duplicated in the laboratory by certain chemical and physical processes. A similar type of change in linen can be obtained by sulfuric acid or heat. OTHERS AMONG US ARE PREPARED TO ENTERTAIN ALTERNATIVE EXPLANATIONS, NOTABLY THE IMAGE HAVING BEEN FORMED ON AN IMPURITY COATING , POSSIBLY STARCH. However, there are no chemical or physical methods known which can account for the totality of the image, nor can any combination of physical, chemical, biological or medical circumstances explain AS YET the image adequately. MODELLING OF IMPRINTS, PROBABLY WITH SIMULATED RATHER THAN REAL BODY FLUIDS, MAY POTENTIALLY OFFER AT LEAST ONE PROMISING DIRECTION FOR FUTURE RESEARCH.
Thus, the answer to the question of how the image was produced or what produced the image remains, now, as it has in the past, SOMETHING OF a mystery, OR AS SOME OF US PREFER TO SAY “YET TO BE DETERMINED”.
We can conclude for now that the Shroud image is that of a real OR SIMULATED human form of a scourged, crucified man. It is not the product of an artist – AT LEAST NOT ONE THAT WAS EXECUTED FREEHAND WITH PAINT AND BRUSH (WHICH WOULD NOT PRECLUDE AN IMPRINTING PROCEDURE) . The blood stains are composed – OR AT ANY RATE SHOW THE PRESENCE – of hemoglobin and also give a positive test for serum albumin. The image – AS WELL AS BLOOD THAT SOME CONSIDER “TOO RED” – is an ongoing mystery and until further chemical studies are made, perhaps by this group of scientists, or perhaps by some scientists in the future, the problem remains unsolved.
—————————————————————————————————————
Note the inexplicable absence of a key descriptor of the Shroud body image: namely NEGATIVE, as in “negative, tone-reversed image, demonstrated by Secondo Pia in 1898”.
Extraordinary. Truly extraordinary, which some some, myself included, might think reprehensible. It’s like describing a London double-decker bus, omitting to mention that it’s bright red, visible from afar.

“Bus? Show me where. I see no bus” (anonymous member of STURP team)
Is it any wonder then that there’s no mention either of the term “IMPRINT”, when STURP could not even bring itself to say “NEGATIVE”.

Penguins displaying STURP’s 360° view
Come to think of it, the term “negative image” gets only a passing mention or two in John Heller’s 1983 book “Report on the Shroud of Turin”. Why? Why??? WHY????????? (I think I know why!).
And you, Mr. Barrie M.Schwortz, have the brass neck to hold up your STURP enterprise and its over-wordy, largely negative conclusions, posing more questions than they answer, to present day scientists as a model of scientific good-practice?
More, maybe tomorrow, dear site visitor (Monday at the latest).
Sunday October 7, 2018
If I had to summarise the numerous failings of STURP in just a few words, (no easy task!) what would they be?
Here’s my first attempt.
STURP, or rather its managerial Godfathers, weren’t merely content to proselytize their own ideas. They tried prematurely to convert initial hypotheses to grand theories and then self-evident fact, like cloth-body distance being a determinant of image density, then proceeding to set ground rules for others.
One does not have to look far to find evidence for what I have just stated. It’s there in the STURP Summary, it’s in Team Leader John Jackson’s published work, it’s in John Heller’s book, it’s in the output from Italy’s ENEA researchers (Government employees!) etc etc
Let’s not mince our words. What we see (and is easy to document) is not just science. (Indeed, there are far too many instances where objective science has been deserted). It’s attempted MIND-CONTROL to varying extents, which even infected non-scientist Barrie M.Schwortz back in February 2012. See the comments he left about my Model 2 (direct scorching from a hot metal template) on Dan Porter’s site.
Link
Did you really think that was science, Mr.Schwortz, to go declaring that “unlike the TS body image, all scorches fluoresce under uv” ? How many different types of scorch did YOU test Mr.Schwortz?
Come to think of it, how many types of scorch did STURP’s scientific recruits test? How many has anyone tested under uv (apart from myself – oh, and ex-BSTS Newsletter Editor Hugh Farey – these last 6 years)?
The answer, as far as I can tell, is zilch!
So, without a single shred of experimental evidence, basing their claims entirely on a reported weak pinkish fluorescence around the scorched fringes of full-thickness burn holes left by the 1532 fire (i.e. NOT experimental scorches, produced under controlled experimental conditions) we see Barrie Schwortz attempting to dismiss not just “scorches” but thermal imprinting generally without a SINGLE SHRED OF EXPERIMENTAL EVIDENCE TO BACK UP THEIR CLAIMS. Instead, there’s a HAUGHTY DISMISSAL OF A NEW LINE OF ENQUIRY – JUST ONE OF MANY IN MY CASE – CLEARLY AN ATTEMPT TO ‘NIP NON-AUTHENTICITY THINKING FIRMLY IN THE BUD’.
Yet it’s thermal, or indeed any kind of IMPRINTING which offers an immediate explanation for the tone-reversed NEGATIVE image, the feature that STURP and others chose to consign to near-oblivion. It can also explain response to 3D-rendering software (no, not unique to the TS, far from it, as anyone with MS Paint can show with intial 2D images that have solid colour!). Oh, and much else besides, but let’s not waste any more time in repeating oneself endlessly, only to be contemptuously ruled out of order by BS and his post-STURP successors).
Despite all of this, Barrie Schwortz would have us believe that STURP was a model of good science, one to be adopted we’re told by present day investigators, 40 years later. Yet all we have seen from pro-authenticity sindonology these last 40 years is a succession of ever-wilder hypotheses, invariably citing fictional radiation, earthquakes, corona discharges etc etc with no back-up data worth speaking of! Call that science?
More to follow, like a quote from Heller’s book, showing his dismissal of thermal imprinting in a few lines without a shred of experimental back-up. (Even legal attorney Mark Antonacci’s later ‘Resurrection of the Shroud” (2001) managed to cite some experimental allegedly anti-imprint evidence, even if science-wise it was totally OTT and irrelevant!).
Back again…
See this slightly abridged passage from Page 203 of Heller’s 221 page book (with thermal imprinting strangely book-ended with acid-induced coloration!):
“Heat can cause the same kind of oxidation as sulfuric acid, but any heat source radiates in a diffuse manner, and cannot account for the resolution or the three-dimensionality seen in the features of the face of the man in the Shroud or the microprecision of the color on the crests of only the straw yellow fibrils.”
(omit short passage)
“There were a few other really strange ideas, such as hot statues, bas reliefs and so on, suggested by non-scientists, but these had long since been examined and rejected, because they could be ruled out – both theoretically and experimentally”.
John Heller’s admirably candid first-hand account of the STURP enterprise had much to commend it (despite his not accompanying STURP to Turin). But that passage I’ve cited was NOT laudable science by any stretch of the imagination. Some might say it was casual and contemptuous dismissal, unbacked by a single shred of illustrative experimental data.
What’s the point of penning a book – supposedly with a science focus – if one omits to provide at least a page or two on the relevant (or even supposedly irrelevant) hard science, point by listed point?
Call that science, Mr.Schwortz, with STURP’s biophysicist John Heller MD pre-emptively dismissing a major line of enquiry, while depriving the reader (who’s shelled out hard cash for his book) of a single detailed reason?
Let’s look briefly now at Mark Antonacci’s longer references to the possibility of imprinting-by-contact (as distinct from fanciful imaging across air gaps):
More to follow…
Back again.
Hooray. Antonacci’s account of ‘Direct-Contact Theories’ starts near the top of Page 63, and continues until halfway down Page 68.
This posting cannot hope to do justice to the entirety of what he has written (and was not intended for that purpose anyway).
But to give a flavour of his style of exposition – streets ahead one might add on what we have just encountered – AND to register some new thinking of mine on the hitherto unrecognized subtleties and potentialities of imprinting-by-contact (depending amongst other things on choice – by fakers I hasten to add – of imprinting medium and how it’s deployed) I’ll annotate the first few paragraphs from Antonacci’s refreshingly detailed ‘take’ on imaging-via-imprinting.
More to follow
From Antonacci:
“A leading proponent of direct-contact theory, STURP scientist Sam Pellicori, suggests the image might have developed not from diffusion but from the cloth coming into direct contact with a body covered in perspiration;body oils; and/or liquid solutions of myrrh, aloes, or olive oil. No traces of these types of organic liquid substances (or any others) have been detected on the linen.”
Here we see the spotlighted author displaying the same blind spot as that shown by Heller, namely failure to consider a SIMULATED sweat imprint, seemingly yellowed with age, of MEDIEVAL FABRICATION. The latter could have deployed an image-formation technique that did not necessarily need to use runny liquids, but instead an imprinting medium of stiffer consistency, one which was subsequently altered by heat to generate the desired straw colour, thus defying simple chemical analysis (as would be the case if amino-carbonyl Maillard reactions were to generate insoluble, chemically-complex high-molecular weight melanoidins, as first proposed by STURP’s Ray Rogers (albeit too late to get a mention in that 1981 STURP Summary!).
From Antonacci:
“A fundamental problem with all direct-contact theories can be demonstrated in a simple experiment by rubbing charcoal over a person’s face and then draping cloth over it. The resulting image will possess no three dimensional information, appear grossly distorted, and bear scant resemblance to a human face.”
So there will be a photograph in the book, right, one that shows the result of doing that precise charcoal imprinting with an obliging volunteer?
But no, there’s not (WHY NOT?) Why is one expected to part with hard cash for yet another pro-authenticity Shroud-book whose author can’t be bothered to perform a simple experiment of his choosing, who expects the reader to go spreading charcoal over a friend or family member (with no mention of how easy or difficult it will be to wash off afterwards)?
I for one was not willing to deploy charcoal, certainly not on my face, and I doubt whether a single reader out there has done so, which means that Antonacci’s claims regarding no 3D response, barely recognizable human face etc have to go unquestioned. Here’s what we see time and time again in the sindonology literature – being expected to take an author’s “severe criticism” on trust, not being allowed to exercise our own visual judgement from photographs or other data, or maybe able to improve on what’s shown.
No, I was not willing to use charcoal. But some years ago I used Nutella chocolate/hazel nut spread – a crude, rough-and-ready imprinting medium- showing that the Shroud’s ‘spindly fingers’, far from being evidence of imaging via internally-generated soft x-rays (thank you for that Dr. August Accetta) were explainable by imprinting, where a stronger more intense image is obtained from flesh that overlies the slimmer non-compressible central bone!
So how would Nutella perform on my own face (later easily washed off) ? Would the result be barely recognizable as a face, with no 3D-response whatsoever in ImageJ or other 3D-rendering software?
Here’s the result, dear reader. Judge (initially) for yourselves. I’ll be back tomorrow with my own interpreation and evaluation.

Left: initial imprint of my own face; sorry about the excess of Nutella! Right: after light/dark inversion in ImageJ, followed by 3D-enhancement. Note the prominently imaged, albeit flattened nose and nostrils and discernible lips.
Late addition (October 10): I have just imprinted all 4 fingers of my left hand onto dry v wet linen using powdered charcoal. The result, both before and after light/dark inversion and 3D rendering is truly spectacular. It shows how effective a fine powder can be as imprinting medium. I’ll display the result if anyone’s interested, but I mean GENUINELY INTERESTED, not merely trying to score pro-authenticity points. (I’m only here for the experimental modelling, i.e. the science, not to respond to sniping and point-scoring).
What the pro-authenticity brand of sindonology, beginning with STURP, has done is to enclose contact-imprinting within a barbed-wire-enclosed firing range, labelled “ENTER AT YOUR PERIL, EXPECT TO BE SHOT ON SIGHT”.
And its present-day chief spokesman has the nerve to tell us that STURP represented science at its very best, a model for us Johnny-come-latelys to emulate.
Did it heck!
STURP was many things, some creditworthy, some not, depending on which of its 30+ participants you choose to select.
The notion that, overall, STURP represented science at its best could not be further from the truth.
STURP was infected from the word go with starry-eyed pro-authenticity bias , one that wasted no time in attemptinmg to sideline or wrongfoot the perceived opposition.
STURP, 40 years ago, and even today, displays the unacceptable face of agenda-driven American free-enterprise…

Newsflash (October 8, 2018)
We interrupt this programme to bring you this newsflash (OK, let’s not go wild: newsglimmer maybe). Here’s a cut-and-paste :
It has just appeared on shroud.com’s commemorative issue marking the 40th anniversary of STURP. See under Internet.
[Editor’s Note: I received an e-mail from avowed Shroud skeptic Colin Berry on May 30, 2018, which included a link to a compilation web page of his research on the Shroud. Frankly, I did not respond to his e-mail nor did I include the link in our June 21, 2018 website update. Shortly thereafter, I received a comment from and had a written exchange with David Goulet, one of our viewers on our Facebook page. With his permission, I am reprinting it below, since it explains why I was initially hesitant to include the link to Colin’s web page.]
-
David Goulet – Robust update! However I would like to recommend that, perhaps at next update, you give a nod to Colin Berry’s website and ongoing experiments that provide a possible man-made narrative for the Shroud. I know Colin is not the most popular Shroud investigator but his research is compelling. His is, imo, the one non-authentic hypothesis that bears serious consideration. If reason is to serve faith, then we must challenge our assumptions and Colin’s site is a place to do that. To ignore the incredible amount of scientific modelling and research he has undertaken would be a disservice to the Shroud.
-
STERA, Inc. – I will certainly consider it for our next update. However, Colin didn’t win himself any friends by launching unprovoked ad hominem personal attacks against other researchers (including me) on a regular basis when Dan Porter’s blog was still active. Disagreeing with a researcher’s conclusions or results is how science advances and is perfectly acceptable, but personal attacks, particularly on deceased researchers who are no longer alive to defend themselves, crosses the line. Sadly, Colin crossed that line regularly.
-
David Goulet – Acknowledged and I appreciate the reticence given his antagonism. My main concern though is that regardless of Colin’s demeanor his science modelling continues to be compelling and innovative. There may be aspects of his work that may even provide insights for pro-authentic researchers – for those with the patience to sift through his site and deal with his truculence.
-
STERA, Inc. – Fair enough. May I quote this exchange? You made a convincing argument and I’d like to publish it with the link.
- David Goulet – Of course. Thx.
- Shroud of Turin Without All the Hype – This is the link to Colin’s web page.
Posted October 8, 2018
I’ll say no more for now, except to remind Mr.Barrie M.Schwortz that one cannot go suppressing criticism of what one perceives as faulty, far less hugely misleading so-called science including in some instances leading figures in STURP simply because they are no longer with us. None of us are immortal. Mortality is a fact of life, a terminal feature of the so-called “human condition”…
Criticizing their hasty conclusions and/or prognostications in no way constitutes what BS describes as “ad hominem” attacks. Indeed it’s arguably an ad hominem attack upon myself from BS to claim I’m the one guilty of making ad hominem attacks!
BS needs to look in a mirror! See for example the way he refers to Professor Luigi Garlaschelli, spotlighting his areligious (“atheist”) take on life and the Universe, one that is shared by hundreds of million others on the planet! I too, btw, regard myself as a (closet) atheist, but consider that largely irrelevant when science is contantly challenged to account for the “mystery”, the “enigma” of the Turin Shroud! (I say the Shroud is a simulated sweat imprint: no, not a real 1st century sweat imprint, but a 14th century SIMULATED sweat imprint, that being a simple science-based message that even now, sindonologists for the most part attempt to stifle or suppress). It’s science and its alleged limitations that is the issue – at least for me. Which is why 7 years of being largely ignored and/or shunned by those ‘challengers of science’ is especially disreputable, showing their true colours some might think, using the TS (partly) as a means of taking a swipe at science and scientists.
PS: thanks to Canada-based David Goulet (keen sindonology observer as well as gifted writer – being author of the interesting funeral parlour-focused “Looney Tombs” ) for his positive take on my approx. 7 year program of Shroud research.
Now back to, er, my critique of Mark Antonacci’s critique (of imprinting-by-contact). More to follow.
Yes, returning to Antonacci (still Page 63 of his 2001 book)…
“STURP scientists Jackson, Jumper and Ercoline attempted to reproduce direct-contact models capable of matching the image characteristics found on the Shroud (ref). They used a plaster mold of a face that was treated with different combinations of liquids and oils at different temperatures and draped with linen representing the Shroud. The experiment identified identified several weaknesses in the direct-contact theory. When the cloth was draped over the face mold that had been coated with in, two different types of shading effects were produced. An image was imprinted only where the cloth and face made contact; no impression was left if the cloth and face were separated by space. Yes, as discussed in Chapter 3, the Shroud body image was imprinted even where there must have been some distance between the cloth and body (for example the sides of the nose).”
The last-but-one sentence is 100% CORRECT! Yes, whether using a real face OR that plaster model one cannot expect to get an image UNLESS there is physical contact. One cannot imprint across air gaps. That is common sense, thus far acknowledged by Antonacci in a modelled system We now move onto the final sentence – kindly fasten your seat belts…
Repeat: “the Shroud body image was imprinted even where there must have been some distance between the cloth and body (for example the sides of the nose”.
Really? How can you be so certain, Mr.Antonacci? Have you tried imprinting off a real face by direct-contact, either with your charcoal, or as did above with Nutella spread?
When I say “imprinting”, I don’t mean simply laying a sheet of linen on top, the default position so beloved of pro-authenticists. I mean imprinting in a medieval context, where the linen is FORCIBLY applied to the face or other parts of the body, to be certain of getting a WELL-DEFINED image ( a scenario you briefly consider in your next paragraph). Under applied pressure you DO get imprinting of the sides of the nose. Why? Answer: the nose FLATTENS under applied pressure, or veers to one or other side, bringing one or both sides into contact with the linen. But there’s a price to pay .. . one gets a somewhat distorted image of the nose, being either flattened or pushed to one side, one or other side of the fairly rigid nasal septum.
But hold on a minute. Haven’t we read something about the nose of the Man on the Shroud looking not quite right? Where was that now?
The ‘flat’ nose in a 3D-enhanced image from Shroud Scope aroused interest on Dan Porter’s site way back. See this link.
But there was an earlier reference to a distorted nose, from a coroner/pathologist no less – STURP’s celebrated if somewhat over-theatrical Robert Bucklin MD (who performed mock-autopsies, dressed in mortuary gear – on TS photographs – see David Rolfe’s ‘Silent Witness’ documentary (googleable). Let’s look out his exact words, shall we? Here they are, not from Bucklin’s 1997 autopsy report (about which the less said the better!) but from the earlier report which John Heller quote on Pages 2 and 3 of his 1983 book:
“The man has been beaten about the face, there is a swelling over one cheek, and he undoubtedly has a black eye. His nose tip is abraded, as would occur from a fall, and it appears that the nasal cartilage may have separated from the bone.”
Well, well, well! The image of the man on the face IS distorted we were told, way back in 1983, possibly earlier by the authenticity-promoting Robert Bucklin MD. (You ain’t seen nothing yet – read his 1997 “autopsy”, performed as if on a real person, or even a photograph thereof, as distinct from an image of unknown means of production, with blood, or “blood” but no unequivocal imaging of wounds, not even in the so-called “scourge marks”. !
But Bucklin’s true-believer interpretation needless to say centred on pre-Crucifixion beating, without a single thought being given to a medieval forgery scenario, one in which linen was pressed up against the nose and face, distorting and flattening the nose, and maybe other facial features too.
Far from being an insuperable problem where imprinting-by-contact is concerned, the nose provides us with a tell-tale forensic signature of a MODELLED pressure-imprinting scenario! But not one using a rigid plaster cast! Oh no, it has to be a real DEFORMABLE face, a real deformable NOSE! So forget all the (overhasty?) claims from Luigi Garlaschelli, Hugh Farey and others that the nose and/or other angular features of the face make imprinting off a real face too difficult, nay impossible. Not so, as I showed back in 2014, using Model 10 (flour imprinting) and relying on nothing more than photoediting software (MS Office Picture Manager!) to intensify the faint natural yellowish-brown tinge of white flour:

Yes, white flour slurry beats Nutella as imprinting agent any day (or powdered flour onto wet linen as an alternative – discussed earlier on this site). Note the slight distortion of the nose, a signature of contact-imprinting under strong applied pressure.
We now get to the part of the Antonacci take on contact-imprinting where the waters get well and truly muddied. How? By a mixing up of “3D response” and “image distortion”, aspects which in my view should have been kept, at least initially in two entirely separate watertight compartments, failure to do which has done a huge amount of damage to the case for non-authenticity/medieval provenance. To say this investigator is severely rattled by the misinformation, started by John Jackson, further perpetuated by any number of commentators, in and outside of STURP, would be an understatement to say the least. Future historians could do a lot worse than look closely at what follows…
The starting point is this picture from Jackson et al, one which Antonacci displays on Page 64 of his book:

Fig 41, Page 64, “The Resurrection of the Shroud” by Mark Antonacci, 2000,
Here’s Antonacci’s accompanying text on Page 63:
“When the investigators pressed the cloth onto those surface points where contact was not made during the natural draping over the face mold, the resulting image was grossly distorted (see fig.41).”
That refers to the image on the left, prior to attempted 3D-rendering.
That passage is followed by this one, referring to the image on the right:
The VP-8 analysis of the direct-contact photographs yielded even more pronounded image distortions (fig.42) which means that direct-contact models cannot produce the correct three-dimensional information.
Gulp! More to follow… much more. It’s not so much what it says, as what IT DOESN’T SAY! Sorry, but science (unlike legal advocacy) does not take kindly to truncated arguments that omit crucial information. It’s just one more symptom/manifestation of agenda-driven pseudoscience!
So what does it fail to say? Answer: it omits to mention that part of a 3D rendering, whether from a face or plaster mold, that is called the SIDES! It omits to mention “lateral distortion” by name, it omits to mention that lateral distortion is entirely avoidable by a simple expedient – at least in a medieval simulation of a 13 centuries old sweat imprint: don’t imprint the sides, that way you avoid lateral distortion!
Are the sides of the face or body visible on the body image of the TS? Answer – NO! A resounding NO!
So let’s be absolutely clear shall we about why that last quoted passage from Antonacci is wrong- spectacularly so. Yes, there is image distortion? And why? It displays lateral distortion? Why? Because the fabric was (a) allowed to make contact with the sides of the mold and (b) the sides of the mold transferred the imprinting agent onto the linen. Result – a distorted image when the imprinted linen was laid flat. But is that the same as saying that the imprinted image failed to respond to the 3D-rendering software? Answer: NO. Compare the image on the right with that on the left and one sees that, despite the lateral distortion, there WAS a 3D response! Look especially at the “hair” on the right, and what does one see? One sees a mountain range in miniature.
It’s not just Mark Antonacci who conflated 3D with lateral distortion. John Heller did exactly the same in his book. Go to the page of photos facing Page 83, and what does one see? One sees a photo with the following caption:
“A VP-8 of a photo of William Ercoline. Note the gross distortion of all the features and the two-dimensional quality of the VP-8 – both characteristics of a VP-8 taken from a 2-D surface. The only exception isthe Shroud.”

Wrong, wrong, WRONG!
Yes, the photo of William Ercoline does show distortion, but it also shows a positive response to the 3-D rendering software.
Why? Because any image with variations in image intensity will respond to 3D software, because that’s what the software does – it promotes 2D image intensity wherever it finds it to apparent 3D, simply by creating an imaginary third (z axis) to initial x and y axes and creating a needle-forest of height bars in place of 2D pixels. (The forest is later smoothed out, given artificial shadowing etc).
Why the distortion? Because photos, paintings etc already contain an impression of 3D by means of angled light illumination, real or imagined by the artist, in the form of shadowing. But the software has no means of distingushing between image and shadow – both get elevated on account of their additional image intensity. Forget all the semantic nonsense that intrudes by use of the term “encoded information” Yes, the software may have a computer at its heart in order to process the multitude of pixel intensity information, but it’s not there to decode, merely to re-display in a new re-mapped form with that third imaginary z axis (aka coordinate), one that merely takes what it finds with no attempt at “decoding” far less intelligent “interpretation”.
So, to summarise: image distortion in 2D renderings, 3D or both, can take at least one or both of two different forms (there may be more).
The first is from shadowing in photographs and paintings becoming elevated as if image, when it’s not. Solution: avoid photographs and paintings. Use IMPRINTS instead (and I say the TS body image is an imprint, not a photograph – or radiation-generated proto-photograph – and certainly not a painting.
The second is from lateral distortion, from attempting to imprint off the sides as well as the flatter frontal planes of face and body. Solution? Don’t. Either keep the linen clear of the sides, or apply one’s imprinting medium to the frontal planes only, keeping the sides uncoated. It then doesn’t matter if the linen makes contact with the sides.
How to ensure that frontal planes only receive imprinting medium? Answer: this investigator discovered two ways. The first, used that flour imorint of my face above, was to make a slurry of flour in water, and paint it onto the parts one wants imaged.
The second, more subtle, is to sprinkle dry powdered flour from ABOVE the recumbent subject as imprinting medium (maybe smearing the subject first with oil to act as weak adhesive) such that flour settles on the frontal (more or less horizontal) planes only, failing to settle on the more vertical sides. Then imprint onto WET linen. Each method has its pros and cons (about which more later).
So what are the prerequisites of an image that renders it responsive to 3D software? Does it require imaging from a real life 3D entity (regardless of mechanism?).
As long ago as Feb 2012, when this investigator was evaluating imaging via direct scorching (from hot metal template) he found that simple items with scarcely any 3D relief (an aluminium pencil sharpener and a metal African bas relief trinket) gave a pronounced response with ImageJ.

“Encoded” 3D, items uniquely responsive to 3D software? Oops, no, the Turin Shroud body image claims that title! Mustn’t muscle in…
What about input images that have no 3D history whatsoever? Do they respond to 3D-rendering software? Surely not…

Still 2D – a graphic with no 3D history whatsoever?
No, it’s now gloriously 3D, and for very simple reasons. The 3D-rendering software converts image intensity to height on a new imaginary vertical axis. Any input with variable image intensity does likewise. No “encoded 3D information” is needed. No decoding of “encoded 3D information” is needed.
Yet as recently as that Pasco conference last year, we were being told how the TS body image was “uniquely responsive” to the VP-8 image-remapping software. No, it’s not, and it’s high time that bit of misinformation ceased being put about, year after year, long after the basic proposition was conclusively disproved, by myself and others.
See the response to one of my postings on the Porter site, the one where I showed that a Model 10 flour imprint responded much the same to ImageJ software as the TS body image from Shroud Scope. Talk about galloping mumbo-jumbo!
Question: how do the results of 3D-rendering compare if computer-generated graphics are compared side by side with imprints from bas relief templates or fully 3D ones?
Answer: it may be there somewhere in my 7 years (approx) of archives. But what’s the point of experimenting further when one is a non-person where pro-authenticity promoting sindonology is concerned? Why waste more time that I have already.
No, I shan’t. Instead I’ll take a leaf from that same body of opinion, going briefly into full-speculation mode, not bothering with anything so tedious as experimental modelling.
Can flour imprinting (my Model 10) deliver a degree of subtlety that is maybe superior to those alternatives lacking any 3D history? Yes, I believe it can, at least in theory, and here’s how. It’s that ability to capture an image of the nose (prominent) AND an image of lower relief (forehead, lips etc) contrary to received wisdom that provided a clue.
More to follow…
Right then, white flour imprinting agent is superior to Nutella. Why? There are several factors that could be listed. Like how easy is it to spread an evenly thin layer over the subject to be imprinted.
(Variations in thickness, if translated into random differences in transfer onto linen would clearly make a nonsense of 3D-rendering, given the latter depends critically on variations of image density that reflect the subject’s real 3D relief).
White flour can be used to give a thin even layer, whether painted on as a slurry (and spread out evenly) or, better still, coated with sprinkled flour, the excess then being shaken off.
Now let’s move on to the final factor, the one I suspect accounts mainly for the superiority of dry white flour, applied to wet linen. It’s to do with differential pressure.
Try this quickie experiment. Press the palm of your hand across your face, compressing your nose sifficiently to feel hand pressure on cheeks, forehead etc. Notice anything?
Note that the pressure on the protuberant nose is greater, considerably greater, than that on the lower relief. The answer is obvious. The force needed to compress/flatten the nose reduces the force on the lower relief!
Here we have what I believe to be the explanation for the spuriosu (and totally unscientific) cloth-body distance factor introduced early on by John Jackson, accepted uncritically by others. It supposed a loosely-draped with air gaps, but apparent imaging across those postulated gaps, leading to the fanciful idea of imaging via some kind of radiant energy. Not so. The cloth was not loosely draped in our medieval scenario. It was firmly pressed against the subject. closing many (but not all) air gaps.
But some relief was better imaged than other, despite physical contact in all cases. How? By the higher relief making the first contact with the linen- leaving a more intense imprint than lower relief, the latter partially protected from application pressure by the higher relief.
In short we have a contact-only imprint model, but one that incorporates the notion of differential application pressure (and subsequent efficiency/inefficiency of medium transfer) due to increasing difficulty to apply pressure to progressively lower relief.
One needs a shorthand to summarise the proposed phenomenon, one of graduated protection with depth from applied manual pressure, creating subtle differences in image intensity, ones that reflect the subject’s own 3D relief, while not preventing a basal 3D imprint as might be seen with simple, shallow bas relief. As I say – subtle, not all or nothing as might be expected from a contact-imprinting model, but one that is nuanced, highly nuanced.
Here’s superlonghand for starters (well, one has to start somewhere):
Contact-only imprinting, but pressure-variable transfer of medium, due to difficulties of access to lower relief on account of subject’s linen-impeding higher 3D relief.
Shorter hand:
Partially obstructed, pressure-modulating contact-only imprinting.
Alternative shorthand?
Contact-only imprinting, but pressure-sensitive for both voluntary and unavoidable anatomical reasons.
Alternative shorthand?
Pressure (not distance) dependent, image-density-variable/obligatory-contact imprinting (no air gaps).
Or: Contact-only imprinting, with pressure and image intensity attenuation arising from template-variable physical 3D-hindrance.
Or: Template 3D-induced pressure-variable image attenuation in direct contact imprinting.
Or: Pressure-variable contact imprinting, with imprint-intensity nullified or attenuated – by template-specific 3D geometry
More to follow…
Image intensity is the same for frontal and dorsal surfaces (cited by pro-authenticity camp as supporting imaging via radiation. Imaging by contact, we are told, would make the dorsal side image more intense – if imprnting-by-contact where the mechanism of imaging).
There’s a simple answer to that argument, cited several times before on this site. TWO volunteers were used for the imprinting, both recumbent, head to head, one face up, the other face down. Both were ‘floured-up’, then covered simultaneously by the same single sheet of wet linen. Both had the linen manually pressed DOWN onto their bodies, yo generate the frontal and dorsal images simultaneously.
Why have one face down? Why not face up, and press the volunteer’s body down into the linen? Answer: in that configuration, previously called ‘LUWU’ on this site – Linen Underneath With Underlay – there is no opportunity to exercise fine manual control over the imprinting process – it becomes entirely passive, with everything out-of-sight. Better to deploy the ‘LOTTO‘ confhguration for both frontal and dorsal imprinting – Linen On Top, Then Overlay. (Overlay optional with LOTTO, less so with LUWU ). It’s also easier to get the two images properly aligned when there are two cooperative individuals, following instructions to edge this way or that until both are perfectly aligned on the long axis.
More to follow
Tuesday October 9
So how should STURP have set about its self-appointed task, it wishing to be seen as scientific, deploying all the 13 process skills of true science (as distinct from merely accruing data with no defined goals or hypotheses worth speaking of?)
First, it should have paid scant attention to that “just a painting” write-off. That can and should have been excluded largely on the basis of the negative tone-reversed body image. Artists do not paint negative images, unless deliberately wanting to portray the ‘look’ of an imprint, in which case they might just have well imprinted rather than painted (especially given the pointers to the “real” Joseph of Arimathea linen, with full-sie naked human body, front v back, no sides, realistic-looking bloodstains in ‘all the right places’ etc etc).
Properly thought through, the aim should have been to set up an alternative credible hypothesis if wishing to face sceptics square-on : not “just a painting” but “just an imprint”. Ay, there’s the rub, as Shakespeare put it.
STURP’s team leader John Jackson wasted no time in interpreting, some might say explanation-pre-empting the image characteristics as those produced not by contact-imprinting, but via some kind of mysterious hitherto-unknown-to-science proto-photographic imaging across air gaps, via undefined collimated, gravity-aligned electromagnetic radiation. (Yeah right, call that science, John Jackson PhD? Is that what they taught you with at that doctorate-awarding naval academy?) Sceptics were immediately faced with the near-impossible task, not of systemtically seeking evidence to clinch an imprinting mechanism, but of near-impossible evidence to DISPROVE Jackson’s fanciful religion-inspired thinking! To think that STERA’s President holds up the STURP enterprise as model for good science! Methinks you should have stuck to the documenting photography, Mr. Barrie M.Schwortz, instead of telling modern day scientists how to do their job. We don’t tell you how to take your photographs?
Is there anything STURP could have done, or indeed did so, to make the best of a bad job – to get the real and RELEVANT hypothesis-driven science on the road, if only tentatively? Answer: YES, in both cases. A start was made, one that is much neglected indeed largely overlooked in so much of the current sindonological literature. And guess what – it used photography – not documenting photography but scientific photography. It was a hugely promising start, given what it revealed about the Shroud body image – at the microscopic level! Thank you STURP’s Vernon D.Miller and fellow “Scientific Photographers”. It could have been used as a basis for scientific modelling, to be done both before (especiallly BEFORE!) or after the actual 5 days spent by STURP in Turin. It can even be done today, once we clear out sindonology’s accumulated clutter of “just a painting” or “supernatural radiation” notions built on their subsiding foundations of sand over 40 odd years.
More to follow tomorrow – with concrete proposals for that much-needed MODELLING of the peculiar Shroud image characteristics – the so-called ‘half-tone effect’, the “image discontinuities”, the “striations”, the ‘second face’ effect, the image-fibre fragility, the identification of the image chromophore et etc etc.
Expect to see a proposed central role for “radiochemical markers’ for both linen AND non-linen components, final destinations tracked by means of autoradiography!!!!
PS: have so far merely hinted at the major (?) proposition being launched, namely that what previously has been seen as a all-embracing cloth-body distance factor is in fact something entirely different that was overlooked by Jackson and others namely a resistance or obstruction to lower relief by first encountered higher relief. That then impacts not only on the map of 2D-imprinted image intensity, but on any subsequent attempt at 3D-rendering
Is there a way of testing that proposition experimentally?
Yes, I do believe there is. Hopefully, MS Paint and ImageJ between them might supply an answer (albeit provisional for the time being). Time now to charge up an ancient largely-retired laptop in the spare room with its downloaded Image J software, MS Office photoediting (for brightness/contrast control) etc. Hopefully there will be something to show for my labours tomorrow.
Be afraid, John Jackson. Be very afraid. Well, mildly discombobulated anyway, given that largely-impenetrable thick skin, nay carapace of yours. (No, we don’t mince our words on this site) .
Science (real ‘tell-it-the-way-it-is-science’ that is ) works via targeted and systematic discombobulation of those folk, scientifically qualified or otherwise, who stick stubbornly and rigidly year in, year out, decade in, decade out – to their quaint outdated notions as to how the real (allegedly miracle- interrupted) world operates.
Yes, more tomorrow… Comments as ever welcome…
Wed October 10th 2018
On second thoughts I think it better to end this posting here, and keep the subtleties of pressure-sensitive/body contour responsive contact-only imprinting for another occasion.
(That’s imprinting with white flour onto wet linen – my Model 10 – NOT with super-sticky Nutella spread onto dry linen I hasten to add)!
Hopefully I’ve said enough to make clear that the air-gap invoking cloth-body distance model of Jackson and others in its countless guises is not by any means the only show in town, and indeed should have been run out of town decades ago. Why? For being shamelessly and outlandishly unscientific. Raymond Rogers, STURP’s chemical team leader, said as much…
Pro-authenticity sindonology is currently raising my blood pressure, as might already have become apparent.

Look carefully: if you’re very observant, you might just be able to spot the three sindonologists in this picture
Time now for me to take an extended break from its incessant undermining of science as I, a retired experimental, model-building, model-testing scientist, understand the term (see that link cited earlier to science’s 13 process skills!).
Science, correction, pesudoscience, ought never to be deployed as a propaganda weapon, used to promote this or that ideology… It cheapens and debases science.
Au revoir (but assuredly not adieu).
Concluding message to the President of the Shroud of Turin (so-called) Education and Research Association from what he refers to as this ‘avowed shroud sceptic’ :
The Shroud of Turin is simply a medieval attempt to mimic the kind of body imprint (sweat and blood) that might have been left by the crucified Jesus on Joseph of Arimathea’s ‘fine linen’ en route from cross to tomb.
Where the take-away message is concerned, nothing more needs to be said. Everything else is detail.
The Shroud of Turin is simply a medieval ‘fake’ memento of something that the Bible states took place some 13 centuries earlier. It’s a ‘faked’ souvenir, no more, no less.
Now then, what was the real purpose of Stonehenge and Silbury Hill (returning to what was this investigator’s secondary, now primary interest)?
No, I won’t supply a link, not being in the business of self-promotion.This retired scientist is merely attempting to quash fatuous speculation, establshing the real facts, such as are presently available.
Message to Vatican: Time now to invite a STURP Mark 2 (40 years post STURP Mark 1) – with more scientists, fewer technologists.
I’d be happy to be part of the team…
Appendix
- Screen grab of the following 2014 Abstract added today, Nov 4, 2018.

It’s needed to supplement the comment I placed on the end of this posting yesterday regarding the somewhat narrow focus when analysed in terms of word counts.
2. Site banner: see how a simulated sweat imprint (my wet hand pressed down onto dark fabric) responds magnificently to 3D-rendering computer software (ImageJ) before and after tone-reversal (negative back to positive image). Remind you of anything? Like those supposedly “unique” and “encoded” 3D-properties of the Shroud of Turin body image?
For a more realistic aged/yellowed sweat imprint, see the many postings on this site since 2014 obtained with the aid of my Model 10 (imprinting off parts, notably head and hands, of a real body (mine!) onto linen with white wheaten flour, followed by heat-development of the image to generate carbon-based and thus bleachable straw-coloured melanoidins via Maillard reactions between wheat proteins and reducing sugars).
Postscript (added Dec 20, 2018)
Here’s a photo I took a few yards from our hotel two weeks ago on the Maipo river valley, western-fringe-of-Andes, approx. 1 hour drive SE from Santiago, capital of Chile. Delicious scenery, wot?
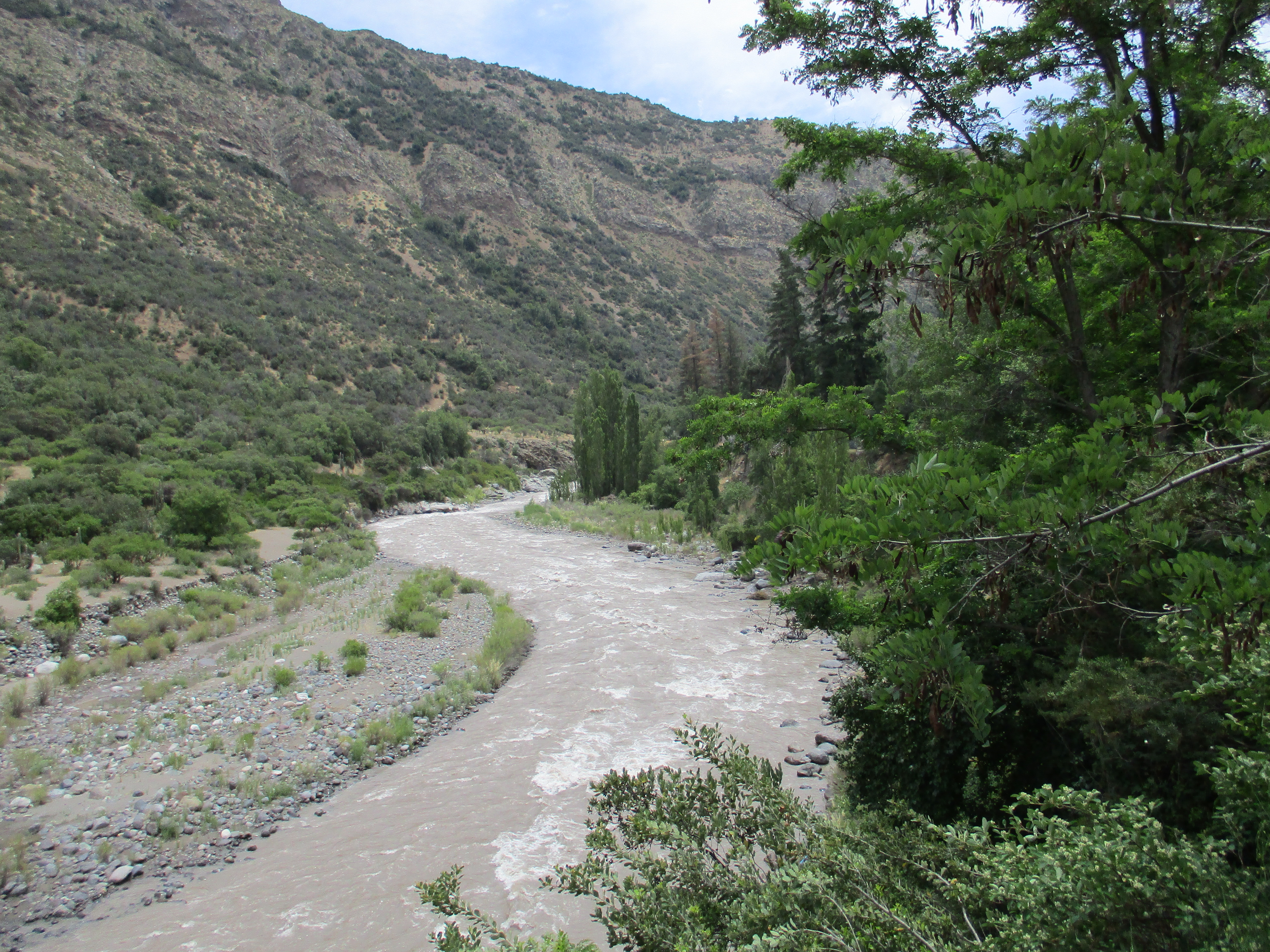
Important postscript (added Dec 27, 2018)
As flagged up several times these last few months, this long-term investigator of the Shroud (7 years anniversary in 3 days’ time ) has been holding off from posting new material these last few months (let’s not dwell on the reasons!). Suffice it to say I’ve been deliberating at length on how best to convey the message that has formed, nay crystallized, in my mind these last 7 years, starting with my Model 1 (“thermostencilling” with charcoal) posted on my sciencebuzz site on Dec 30, 2011.
Back in October, I suddenly realized what I’d overlooked to do, back in 2011 (see “Late addition, October 10” this posting, highlighted with red font). Had I done it, there’s a real possibility I could have jumped straight from Model 1 to current Model 10. Drat! I should have IMPRINTED with charcoal (NOT painted!).
I now have (finally!) a handle, not only on resolving the enduring ‘enigma’ of the Shroud in research terms, but conveying the essence of the oh-so-simple solution! Expect a posting (maybe preliminary) on the 7th anniversary of my baptism-by-charcoal this coming Sunday (Dec 30, 2018). In the meantime, here’s the key image that will be displayed prominently:

The key buzzword? Why, POWDER (as in powder imprint) of course!
Probable title of my next posting:
“Turin Shroud: simply a one-off medieval powder imprint. ( So, please, let’s now draw a line under decades of pseudoscience.)”
Further reading: http://colinb-sciencebuzz.blogspot.com/2019/08/re-that-misnamed-so-called-shroud-of.html